Let’s build the future in manufacturing.
There is more to manufacturing than you think.
Start building your future now.
0
*Georgia Mountains Region, 2022
0
*Georgia Mountains Region, 2022
0
*Georgia Mountains Region, 2022
0
*Georgia Mountains Region, 2022
Start building your future now.
Find available posts for different types of manufacturing work in our region.
Learn how work-based learning programs have changed the future for high school students.
Upcoming Events
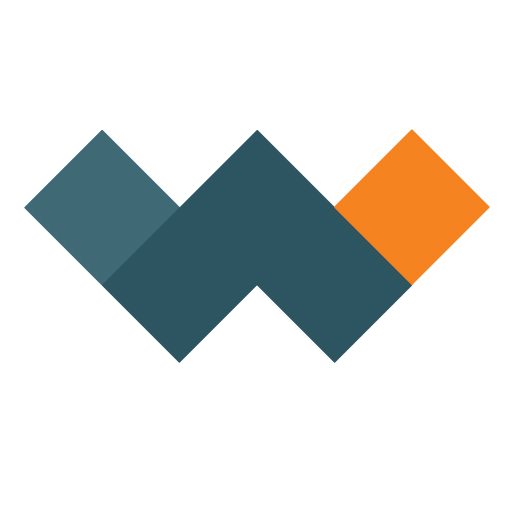
August 14, 2025
LEAD Fall 2025 North Georgia Technical College, Currahee-Toccoa Campus
LEAD Fall 2025 North Georgia Technical College, Currahee-Toccoa Campus
SAIL Fall 2025 at Lanier Technical College, Gainesville Campus
July 29, 2025
Manufacturing Sector In Person Meeting
September 10, 2025